Although unique to the G40 model, the G40 engine (code PY) is closely based on the standard 1272cc Polo power plant. This conventional 4 cylinder water cooled design uses a cast iron block and alloy head. In the G40 it is transversely mounted, coupled to a manual 5 speed gearbox via an uprated clutch. Its main difference from other Polo engines is the addition of a supercharger to significantly boost power output.
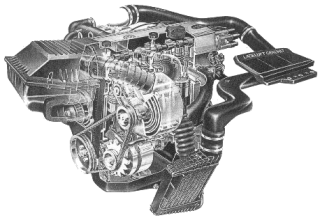
Engine Management
Engine operation is controlled by an Electronic Control Unit (ECU). This ECU is a G40 specific version of the VW/Bosch Digifant Mk1 system. Similar ECUs are used on other VWs including the G60 powered cars and the Mk3 Polo GT. The Mk3 G40 Digifant is based on a Motorola MC68HC11 microprocessor and its control program is stored in a 32K byte EPROM device (type 27C256). This EPROM is normally referred to as the 'chip' and its contents include the ignition and fuelling maps that define the engine characteristics. 'Chipping' involves replacing the EPROM with an aftermarket version using new maps intended to improve performance.
The ECU uses a number of sensors to determine the engine's current operating conditions; knock sensor, distributor Hall sensor, air temperature sensor, coolant temperature sensor, MAP sensor, Lambda probe (oxygen sensor), throttle closed position (idle) switch, and throttle fully open switch. The signals from these sensors are then used to determine the appropriate fuel and ignition timings from the ECU's maps.
Cylinder Head
The alloy head uses a single overhead camshaft driven by a timing belt to operate 8 valves via hydraulic tappets. The use of a supercharger provides adequate power without needing the additional complication of a 16 valve head. To prevent problems with detonation the compression ratio is reduced to 8.0 to 1.
Air Intake and Supercharger
Cold air is fed to the air filter housing from an intake behind the driver's side headlamp. The intake ducting is specially shaped to reduce induction noise. The air is fed through a paper filter before entering the 40mm G-Lader supercharger. (Note that there is a restriction in the outlet pipe of the standard air filter housing.) It is essential that a good quality filter is used as the supercharger can be easily damaged by small particles; the engine should never be run without a filter. The supercharger compresses the air and feeds it to an air cooled intercooler located next to the charger behind the grill. (The intercooler inlet includes a coarse wire mesh filter to protect the engine in the event of a major supercharger failure!) The process of compressing the air heats it up and the intercooler removes this heat and so increases the air's density. The compressed and cooled air is then passed to the throttle.
The throttle system incorporates a bypass valve so that under normal operation any air excess to the engine's requirements is returned to a second supercharger intake (which is directly connected to the main supercharger intake from the air filter). On its way back the air pipe passes through the cam cover. This is purely for convenience of routing. Under normal conditions the air pressure is therefore low and supercharger is doing very little work. Fuel consumption is correspondingly low.
When the throttle is fully opened a mechanical linkage closes the bypass valve and the excess air from the supercharger causes the intake pressure to rapidly rise. The engine then operates at full boost and much higher power is available. If a boost gauge is used to monitor manifold pressure it can be seen that pressure is normally partial vacuum like a conventional engine (also allowing the vacuum servo to operate!) but builds rapidly to positive pressure when the throttle is fully depressed.
Dual 'V' belts are used to drive the supercharger from the crankshaft pulley as the loading is quite high when at full boost. As the supercharger displaces a fixed volume of air on each revolution and it is directly driven by the engine, the boost pressure available when the throttle is depressed is largely independent of engine speed. This produces a very good throttle response from any speed without the 'lag' associated with a turbocharger. A smaller pulley can be fitted to the charger to increase its speed relative to engine speed and so increase boost and performance (at the expense of supercharger life).
Fuel System
A 42 litre capacity fuel tank (approximately 9 gallons) is mounted beneath the rear seat. A lift pump inside the tank (running immersed in petrol) supplies the main injection pump. This pumps the fuel to the engine via a large petrol filter. The injection pump and filter are mounted next to the petrol tank by the driver's side rear wheel. When it reaches the engine bay the fuel pressure is controlled by a regulator which feeds the fuel rail. Excess fuel is returned to the tank. The pressure regulator is arranged such that the fuel pressure in the rail is maintained at a constant level relative to inlet manifold pressure. This ensures that the relationship between the amount of fuel injected and the amount of time for which an injector is held open remains constant, and so allows the ECU to accurately control the mixture under all conditions. Fuelling is by multi point injection (MPI) where a separate injector is provided close to each inlet port. All injectors are opened simultaneously under electronic control from the ECU.
Fuel metering is controlled by the ECU by adjusting the time for which the injectors are opened. In the Mk3 G40 the mass of air entering the engine is calculated using a 2 bar MAP (Manifold Absolute Pressure) sensor in the ECU. The MAP sensor is used to measure the air pressure in the manifold (after the throttle valve). Working on the principle that the volume of air in the engine is the same on each revolution the mass of air can be calculated from the measured absolute pressure. (The earlier Mk2 G40 Digifant used an air flow sensor mounted on the air filter housing.) The appropriate amount of fuel is then injected based on the ECU fuel map with adjustments made for the signals from the air temperature sensor, coolant temperature sensor, Lambda probe, idle switch, and full throttle switch.
Ignition System
Ignition timing is provided by 4 cut outs in a rotor mounted inside the distributor, which is driven at half engine speed off the end of the camshaft. As each cut out passes between a Hall effect sensor and a fixed magnet, a signal is sent to the ECU. This defines the basic firing point for each cylinder and adjustments are made electronically by the ECU for different engine speed and load conditions. Note that the distributor position still controls the basic timing, and must be set correctly. Current through the ignition coil is electronically switched by the ECU to generate the ignition sparks. The dwell time used (time for which coil current is flowing) is constant so that the spark energy remains the same regardless of engine speed. Ignition spark distribution is controlled by the rotor arm position within the distributor cap and the ECU does not know which individual cylinder it is firing. Spark plugs are platinum type (W5DPO) specifically designed for forced induction applications. The signal from the distributor Hall effect sensor is also used to initiate opening of the fuel injectors.
This ignition timing is run close to the point where detonation ('pinking') occurs for maximum power. The ECU uses a knock sensor mounted on the engine to detect if detonation is occurring and will automatically retard the timing when necessary. As a consequence timing will be automatically adjusted for different fuel octane ratings and the car will run happily on 95 RON or 97/98 RON unleaded. (Lower octane fuel may therefore result in a slightly reduced power output).
Idle Control
Idle is achieved by an idle bypass valve which allows a controlled amount of air from the supercharger to bypass the closed throttle valve. The bypass valve is operated by the ECU when the idle switch indicates that the throttle is in the fully closed position and the engine speed is within the idle range. A CO adjustment pot allows small adjustments to be made to the CO level at idle. If when decelerating, the throttle is detected as closed with engine speed above idle range, the ECU stops opening the injectors to conserve fuel.
Electronic Rev Limit
The ECU controls the maximum allowed engine revs by no longer firing the fuel injectors if it measures engine speed above the 6500 rpm limit. When the revs subsequently drop the injectors begin to operate again. Aftermarket chips usually increase this rev limit significantly.
Cooling System
The cooling system is a conventional type controlled by a thermostat. It is similar to other Polos except that the G40 uses a larger radiator. Additional cooling is provided by an electric 2 speed radiator fan, operated directly by a sensor fitted on the radiator. The water pump is driven from the cambelt with belt tension set by rotating the water pump body. The ECU monitors coolant temperature and allows for cold start conditions effectively providing an automatic choke. Despite the relatively high engine output the G40 is not prone to overheating. The correct G11 coolant mixture is essential to prevent corrosion of the alloy head.
Charging System
The alternator is driven by the twin belts used to drive the supercharger. It is mounted beneath the supercharger. The alternator position is fixed and drive belt tension is controlled by adjusting the supercharger position.
Lubrication System
The oil pump is driven from the crankshaft and uses a spin on type oil filter. No oil cooler is fitted. An oil take off on the head feeds the supercharger bearings with a return pipe to the block just above the sump. A good quality oil and regular changes are required to ensure the supercharger remains in good condition.
Emissions Control
All UK G40s were originally fitted with a catalytic convertor to reduce exhaust gas emissions although early models do not require this for the MOT test. A Lambda probe (oxygen sensor) is mounted on the catalytic convertor. The probe is electrically heated to allow it to quickly reach its required operating temperature. The ECU uses the signal from the Lambda probe to maintain the correct fuel/air mixture for the catalytic convertor to operate. Cars fitted with a catalytic convertor must only be used with unleaded petrol as leaded petrol (or LRP) will damage the catalyst material.
To reduce hydrocarbon emissions the fuel tank filler is sealed. Petrol that evaporates while the car is not being used is absorbed by the carbon in a canister found under the air filter housing. When the car is running the engine vacuum operates a purge valve mounted on the rear of the air filter housing. This allows the stored petrol vapour to be drawn into the engine via the supercharger intake where it is eventually burned. (This system probably also acts as the breather for the petrol tank).
Vapour produced by hot oil and combustion gases that get past the piston rings cause the pressure in the crankcase to build up. The crankcase breather system allows this excess vapour to escape. This consists of a dome shaped oil separator at the back of the block followed by a one way valve from where the vapour is fed into the supercharger intake (into the pipe between the throttle bypass valve and cam cover). Rather than being released directly into the atmosphere the vapour is therefore first burnt in the engine so reducing emissions. Note that this breather system commonly blocks up on the G40 resulting in leaking oil seals and oil being forced out of the dipstick tube.
Engine Fault Detection
The ECU has the capability to detect out of range readings from the various sensors. It will use a 'get you home' default value when a sensor fault is found. There is a diagnostic connector for the ECU situated under the passenger side glove box. With the appropriate VW test equipment this can be used to report engine fault conditions.
Nick Dilley